Knowledge Base
Types of Mold Release Agents: A Complete Guide to Choosing the Right Solution
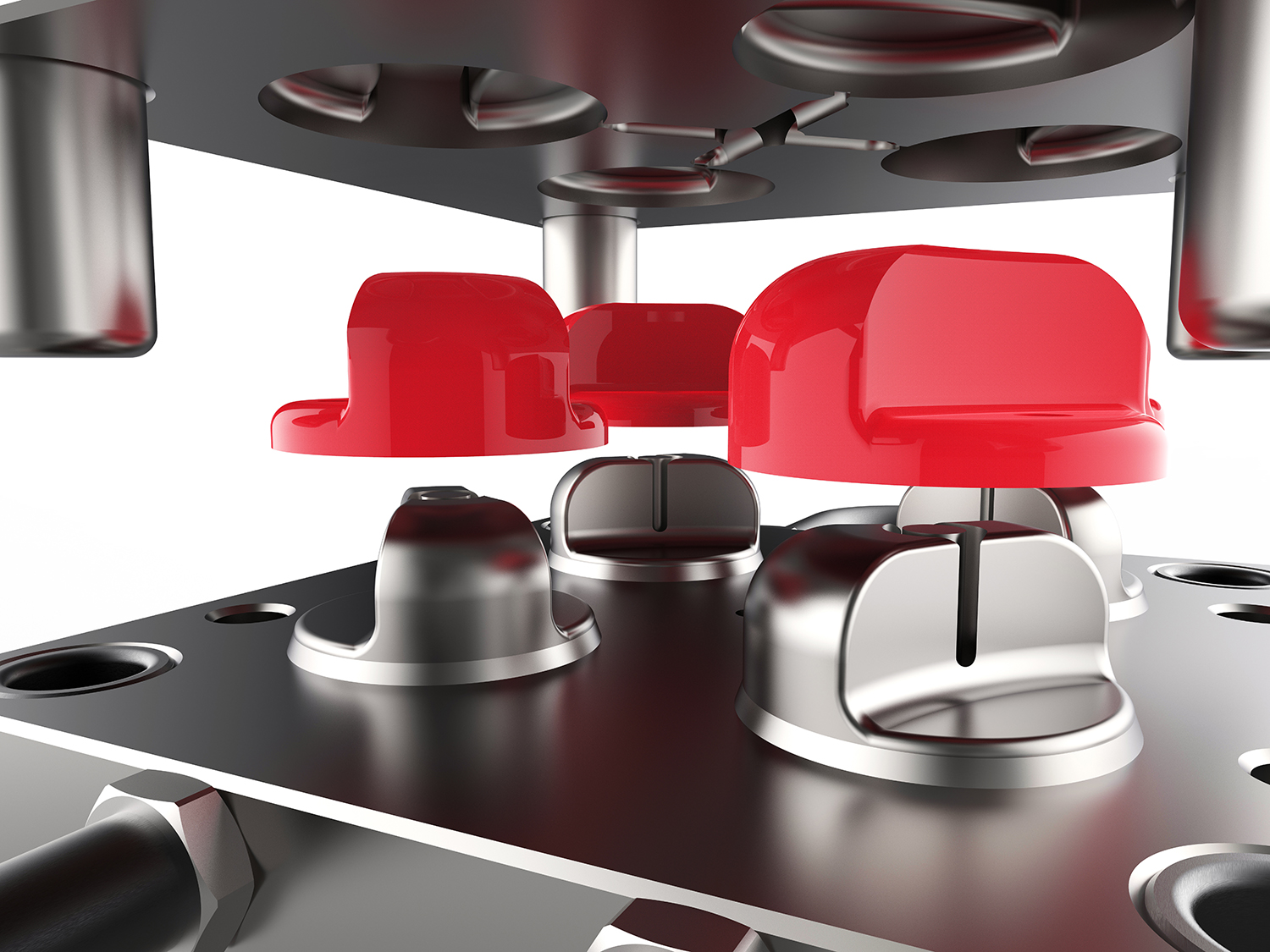
Learn more as you explore the breakdown of various types of mold release agents, highlights of their chemical compositions, modes of action, and practical applications. We'll also explore common categories of selection criteria, including industry, chemical state, and formulation, to help you find the right fit for your specific molding process.
Understanding the Core Types of Mold Release Agents
Choosing the right mold release agent is essential for producing clean, defect-free parts and running your molding process efficiently. Different types offer unique benefits. Some prioritize ease of application and multiple releases, while others focus on surface quality or compatibility with post-molding processing. Understanding these core types helps you select the best fit for your specific application.
1. Sacrificial Release Agents
Sacrificial release agents form a barrier between the mold surface and the molded part, which must be reapplied before every cycle. These agents are ideal for applications where film formation and ease of release are prioritized over cycle time efficiency. Though they increase downtime due to frequent reapplication, they are often necessary for complex geometries or molds that require a high-gloss finish.
These are typically found in solvent- and water-based release agents with distinct benefits and drawbacks. Solvent-based agents offer fast evaporation and excellent surface finish, while water-based versions are more environmentally friendly and emit fewer volatile organic compounds (VOCs).
2. Semi-Permanent Release Agents
Semi-permanent release agents offer multiple releases per application, significantly reducing the number of interruptions during production. These products chemically bond to the mold surface, creating a durable, thin coating that withstands repeated molding cycles. This type is particularly valued for minimizing cycle times and improving overall productivity.
Due to their robust performance, semi-permanent agents are commonly used in high-output environments, such as automotive composites, aerospace components, rubber molding, and rotational molding.
3. Internal Mold Release Agents
Unlike traditional release coatings, internal mold release agents are incorporated directly into the material being molded. This allows the release functionality to be uniformly distributed throughout the part, eliminating the need for surface application. These agents are especially useful in thermoplastics, polyurethane, and thermoset systems where maintaining surface aesthetics is critical.
However, internal release agents must be compatible with the base resin and can sometimes interfere with post molding processes like painting, coating, or bonding.
What's Inside Matters for Chemical Bases and Formulations
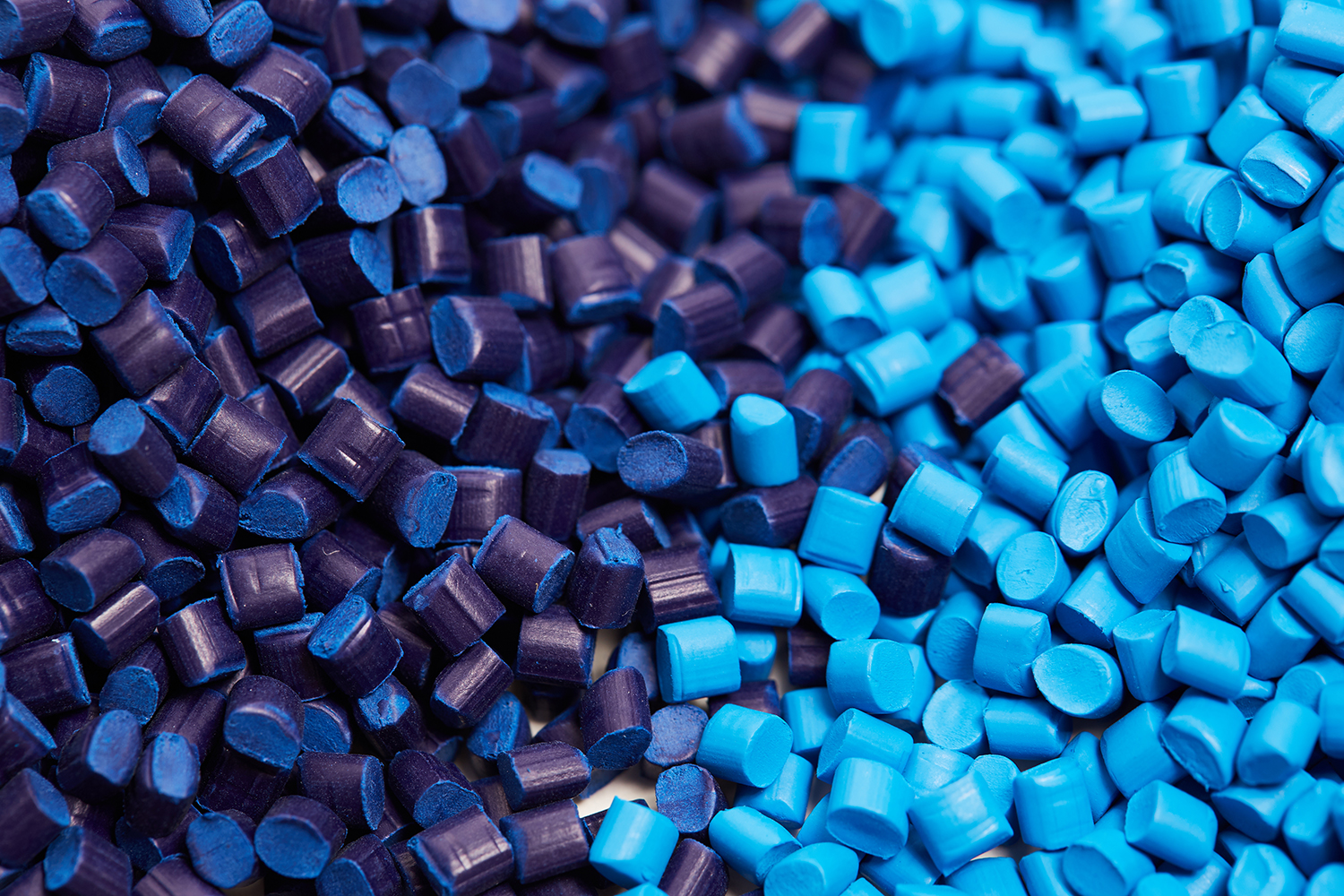
The chemical composition of a mold release agent, whether solvent-based, water-based, or carrier-free, plays a crucial role in its performance during molding operations. Each formulation affects drying time, environmental impact, residue levels, and compatibility with different materials.
By understanding what's inside, you can choose a release agent that aligns with your production needs and regulatory requirements.
Solvent-Based vs. Water-Based
The choice between solvent-based release agents and water-based release agents often hinges on environmental compliance, surface finish requirements, and drying time.
- Solvent-Based Release Agents: Provide rapid drying, excellent surface coverage, and smooth part release. Ideal for intricate molds or when high gloss is required. However, they pose health and safety concerns due to high VOC content and flammability.
- Water-Based Release Agents: Eco-friendly and safe to use, these are increasingly popular due to regulations around volatile organic compounds. Though they take longer to dry and may require heated molds to cure or cross-link, modern formulations have significantly closed the performance gap.
Carrier-Free Release Agents
These products are concentrated and free from water or solvent carriers, reducing overspray and providing a clean working environment. Carrier-free release agents often produce minimal residue and are popular in industries where contamination must be tightly controlled, such as electronics or medical device manufacturing.
Silicone-Based Release Agents
Known for their excellent lubricity and versatility, silicone-based release agents can be used in various applications, from die casting to rubber molding. They are often available in sacrificial and semi-permanent forms and are valued for producing a high-quality finish on molded parts. However, their slick residue can interfere with secondary operations and may not be suitable for all molding processes.
Paintable Mold Release Agents
When silicone is a concern due to electronics applications or where the molded part is decorated—such as hot stamping, pad printing, painting, or metalizing—using a paintable mold release after molding saves significant post-molding time. Yes, paintable silicones are available! Speak to a molding expert today to learn more!
Choosing by Industry and Application
The best way to find your ideal mold release agent is to match it with your industry-specific needs. In our online store, categories are divided to help you explore what works best:
Industry
Different industries require different formulations. For example:
- Composites may benefit from semi-permanent, solvent-based agents to maintain fiber orientation and reduce surface defects.
- Plastics often require silicone-based options for ease of ejection and gloss control or Paintable versions where the part is decorated after molding.
- The rubber and tire industries may rely on high-durability coatings that resist heat and abrasion.
Chemical State
You'll choose between aerosol, liquid, gel, or dry formulations here. Each offers unique application methods:
- Aerosols provide convenient and consistent coverage, especially on small or intricate molds.
- Liquids are great for bulk applications using spray systems.
- Gels enable precise manual application to specific mold areas.
- Dry release agents offer minimal residue, and are useful for cleanroom or post-processing-sensitive operations.
Type of Mold Release
This category helps you match your process to the right formulation, semi-permanent, sacrificial, internal, or specialty coatings tailored for unique substrates or process conditions.
A Quick Look at Performance Factors
When evaluating types of mold release agents, keep these critical qualities in mind:
- Durability: How many cycles can you run before reapplying?
- Compatibility: Does the agent interact safely with your resin system or affect the part’s ability to be painted?
- Residue: Will it leave behind unwanted deposits that could damage tools or parts?
- Safety and Compliance: Are VOC levels acceptable and safe to handle in your environment?
- Ease of Application: Is the method practical for your scale and equipment?
Ready to Find the Right Mold Release Agent?
With so many mold release agents available, ranging from solvent-based to water-based, sacrificial to semi-permanent, and everything in between, it's essential to match your agent to your specific molding operation, material, and production demands. Whether you need a high-gloss finish, reduced cycle times, rust prevention, or eco-friendly compliance, there's a tailored solution.
At Stoner Molding, we make it easy to find exactly what you need. Our intuitive online shop allows you to browse by industry, chemical state, or release agent type, so you spend less time searching and more time producing.
If you need help, our friendly customer service team is ready to answer any questions you might have. You’ll find our high-performance mold release coatings are engineered to improve efficiency, enhance part quality, and extend mold life. Explore our wide selection today and take the guesswork out of mold release.
Shop Now
Unlike many mold release brands, Stoner Molding Solutions formulates, manufactures, and distributes our own products. Check out our full line of mold releases, sealers, cleaners, rust preventatives, and lubricants. In stock products are ready to ship now!