Blow Molding
Inflate Your Goals With Blow Molding
When creating hollow plastic products with complex geometries, You might struggle with demolding, lubricating, or managing the process. Your difficulty is our problem, and we want to help you experience smoother molding production. With our expertise, products, and industry knowledge, you can receive service that will give you a better experience all around!
Plastic low molding is a beneficial process used throughout dozens of industries. From chemical containers to recreational toys and equipment, blow molding has given millions of consumers access to valuable products. But you might not know how to make the most of this technique or want to know other ways to employ it for your production. Read on for an in-depth look at the process, and contact our experts to learn how our mold sealers, releasers, and cleaners streamline every facet.
The Plastic Blow Molding Process
Thanks to a simple general structure, the Plastic blow molding process is relatively customizable. This method can be used with many different kinds of plastic, providing a flexible process that can create products with various qualities and benefits.
Preparing and Mixing
The first step in most molding processes is mixing and preparing the charge. The plastic pellets and granules are mixed with any alloying materials that might be needed to impart bulk, structure, or specific qualities like chemical or water resistance.
Melting and Extruding
The extrusion process uses a long corkscrew to mix, grind, and ultimately melt the mixture. Thermoplastics are simple to melt and use in this method. This method produces an evenly extruded plastic tube that is malleable for the next steps.
Blowing and Forming
This extruded tube is typically clamped at the bottom to seal it, then inflated via a high-pressure air stream. This step inflates the plastic structure, filling the cavity that provides the shape for the product. The plastic is held in place until set enough for ejection.
Ejecting and Cooling
The final few steps can be more varied than the first, but once the item is ejected from the die cavity, it is trimmed of excess material and released. The material typically cools enough to set in the die, but more testing and secondary processes follow demolding.
These are the four general steps to blow molding that you can expect from nearly any production line that involves the process. Some production lines will include leak tests to ensure water or air-tight construction. After every molding cycle, the mold cavity should be cleaned in order to ensure smooth production.
Drawbacks and Benefits of Blow Molding
This method of molding isn’t perfect, but it can provide you with ample benefits to consider throughout your process planning. When you think of adding plastic blow molding products to your company’s inventory of products, you should take the time to look over the pros and cons of this valuable method of plastic forming.
Pros
- Cost Effective: The blow-molding process can provide large-scale manufacturing with a flexible and efficient production method. There is little waste, rapid production, and low costs.
- Flexible: A wide range of materials and designs can be used in blow molding, making it suitable for a wide range of products. The simple process can be tailored to specific needs that other methods might struggle to meet.
Cons
- Less Precision: Blow molding doesn’t have tight control over things like shape, wall thickness, and other fine details, which might require compression or other molding methods.
- Material Limits: While many plastics are used in blow molding, the low-temperature and high-pressure processes exclude certain materials. This may require further research into your needs and plastic supply.
This list of the benefits is not exhaustive you might experience for your specific production. You might notice that plastic blow molding avoids unsightly seams in a way that suits you, for example. But these are the most general and commonly enjoyed benefits and the most often seen difficulties. We can help you nail down the details with a conversation about what you need and expect in your process, so call our experts today!
Types of Blow Molding
Several methods of blow molding can provide unique benefits and results. From cleaner releases to faster production cycles, you should consider if these processes might be helpful to your production line.

Extrusion
Extrusion molding is the standard and follows the above explanation of the blow-molding process. It involves inflating the materials in a cavity with the necessary shape and structure. This type is often seen in creating bottles, like those for water dispensers.
Continuous
Continuous extrusion molding is standard in high-volume production facilities, and mold halves are used to cut cleanly through the extruded plastic. This allows multiple molds to rotate through use and demolding continuously.
Injection
Injection blow molding utilizes a pre-blow injection mold containing the blow rod. This ensures an evenly distributed plastic shell that will be blown. By injecting the plastic into this mold first, you can prevent thin spots and wall failures in your end product. However, the injection phase requires the removal of excess plastic, resulting in less efficiency.
Stretch
Stretch molding is similar to injection but can be done only with extrusion machinery. This process simply uses a stretch rod to apply pressure in a second direction. This bilateral stretching results in ‘biaxially oriented plastic,’ which aligns the polymers for better mechanical performance. But this multi-step process requires more expensive machinery.
There are other sub-categories and formats of blow molding, but these are the methods most common throughout the plastic molding industry.
Plastics Used in Blow Molding
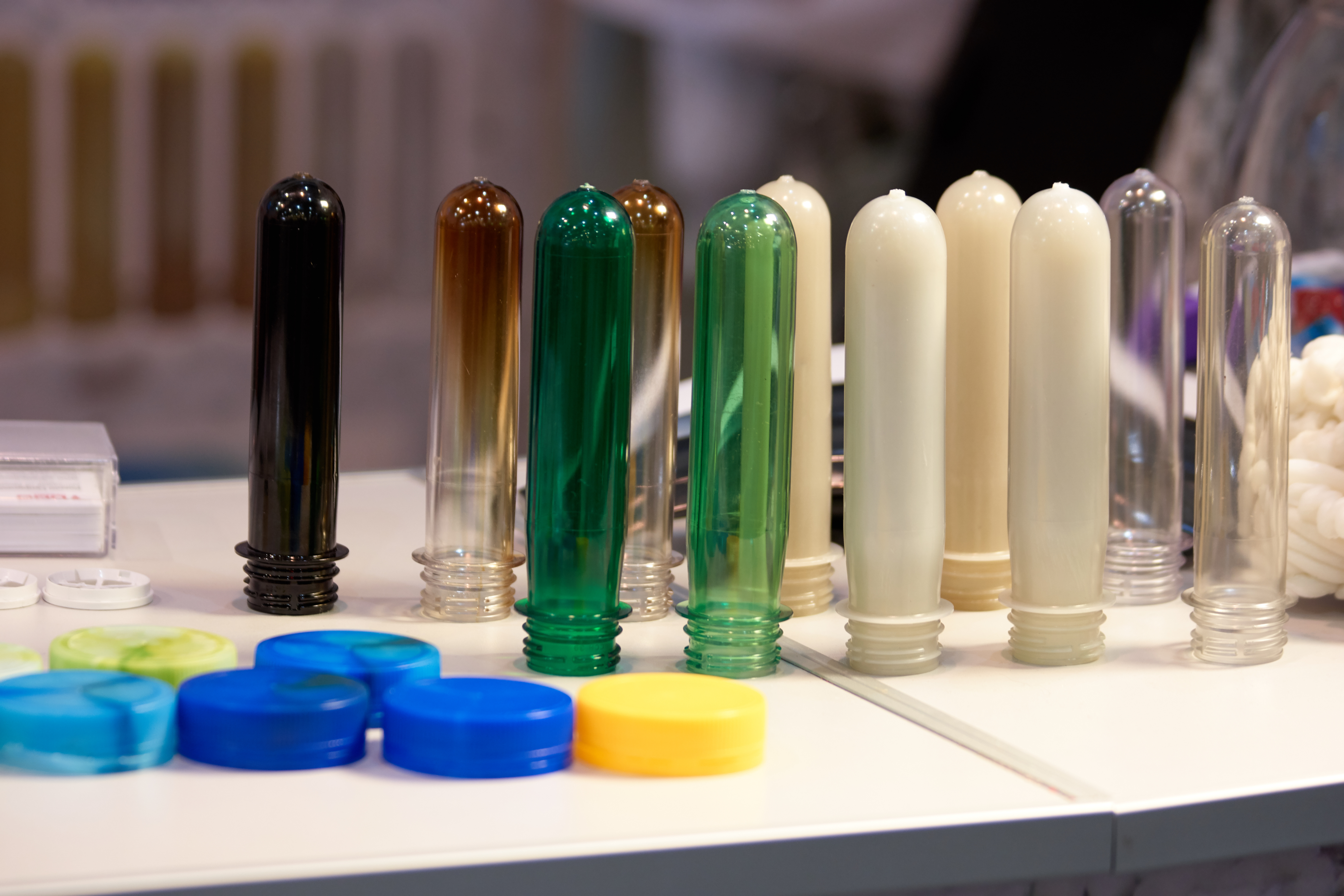
Lastly, let's look at the plastics most commonly used in plastic blow molding products. As a method of thermoplastic molding, the most popular thermoset plastics are commonplace, such as:
- Polyethylene (PE) – An easy-to-process material with low cost and excellent qualities such as no odor, toxin-free, water, and electrical resistance. It comes in high and low-density formats with slightly different strength and durability profiles.
- Polyethylene Terephthalate (PET) – Biaxially oriented PET is most commonly used for carbonated beverage bottles since it has low CO2 permeability. However, it is relatively water-absorbent and needs treatment before extrusion.
- Polypropylene (PP) – Though polypropylene is susceptible to UV damage and oxidation, it is very malleable and can be created with higher tensile strength, hardness, and temperature resistance.
- Polyvinyl Chloride (PVC) – PVC takes on stabilizers and other additives very well, becoming more rigid or flexible as needed. However, PVC can release harmful acids, toxins, and pollutants during processing and degradation, which is why the FDA and EPA regulate this material more.
- Nylon/Polyamide (PA) – Nylon is incredibly tough, resistant to solvents and chemicals, and can be made resistant to heat. We commonly think of nylon as a clothing fiber, which is very common in automotive parts and fuel tanks.
- Polyurethane – This material is used widely throughout many industries thanks to its easy-to-use nature. Medical, recreational, and even automotive equipment all come from polyurethane molding.
Solve Your Production Problems With Stoner Solutions
If you are a molding operation or have decided to produce your own blow-molded plastic products, you should know how complex the process can be. Between the machinery, the materials, and the formulas, even before production begins, you can develop a headache. Come to us for products to help you get the most out of your plastic molding production.
We have the products you need, from mold sealers that keep your products coming out smoothly to mold cleaners that remove the most stubborn residue. Call today to discuss with our most knowledgeable and insightful experts, who will know which products will fit into your process for maximum productivity.