Thermoplastics
Enhance Your Plastic Molding Process with Quality Products
When molding plastic materials, you need the finished product to release quickly with minimal molding defects and a consistent finish. However, when inferior mold releases cause parts to stick to the molding surface or impact the product's dimensional
stability, you waste time and money by having to scrap the parts and mold them again. Your thermoplastic and thermoset molding operations deserve better products.
Every molder wants to get as many releases as possible from each application—with less downtime and waste. That's why we at Stoner Molding Solutions have been creating molding solutions for the thermoplastics industry since the 1950s. We work closely with the Plastics industry to create ground-breaking products that reduce scrap and increase productivity.
How Our Plastic Molding Products Benefit Your Production Process
Why would you spend your money on a product that doesn’t directly improve your process? The bottom line is that you want to spend less while producing more. Our high-performing mold release agents for plastic molding, along with our mold cleaners, rust preventatives, mold sealers, and mold lubricants, are specifically formulated and Engineered for the thermoplastics and thermoset industries. Your plastic molding production line can enjoy the benefits of :
- Optimized cycle time
- A consistent surface finish
- Reduce or eliminate post-mold prep work before gluing, painting, metallizing, or welding
- Minimized mold flow lines
- Reduced scrap parts and lower production costs
Want to Try a Sample Before Your Purchase?
We know that you may be a bit skeptical about trying a new product to improve the productivity of your thermoplastic molding operations. But we are also a global leader in molding releases, flow promoters, mold cleaners, and other mold maintenance
products. Just like dozens of other molding companies, you will receive massive benefits for your plastic molding process if you use these products.
These products will improve your final creation and increase both productivity and profits. We are so confident about the products that we would like to offer you a free sample upon request to prove how incredible our products are! Give us a call and we will help you find the right product that will provide the best outcomes, and send you a free sample to prove it!
Industries Worldwide Rely on Our Release Agents
No matter what type of thermoplastic molding you do, we have a molding product for it! From mold releases with silicone and non-silicone formulations that provide an easy release to lubricants that reduce friction and make molding easier, you can count on Stoner Molding for several molding processes.
Electronics
Electronic cases, components, and cables all use thermoplastic’s incredible durability and insulation qualities for their best results.
Transport
Durability and chemical resistance maximize safety and lifespan for aeronautic, nautical, and automotive parts manufacturing.
Medical
Medicine products of all kinds can be made with thermoplastic molding, from pill bottles to heavy-duty x-ray equipment.
Food and Drink
Food and beverage industries rely upon thermoplastics for a massive array of storage, handling, production, and packaging purposes.
Construction
The construction industry makes frequent use of molded plastic goods in order to provide you with longer-lasting and safer homes.
Injection Molding
The thermoplastic injection molding process is ideal for high-volume, mass-produced products requiring thousands or even millions of parts, such as toys, kitchen utensils, medical devices, surgical equipment, bottle caps, and more. It is typically a cost-efficient, high-output, low-waste, and versatile endeavor. Challenges can come when thermoplastic injection molding machinery breaks down from excessive wear and tear. Our products help avoid these costly repairs and the downtime that will harm your bottom line. These challenges are why it's crucial to maximize mold performance with Stoner mold products.
Rotational Molding
Combining high temperatures and rotational movement, rotational molding can easily form an even-walled thermoplastic or thermoset component. Some products formed through rotational molding include Kayaks, coolers, bins, tanks, containers, road
cones, and more. Rotational molding produces high-strength parts with very little waste, though it is a slower process than some other plastic molding operations. Choosing a mold release agent for plastic that keeps rotational molding operations moving
efficiently is the key to success.
Extrusion Molding
While other plastic molding processes moves plastic into a mold, extrusion moves melted plastic directly through a die. The die's shape determines the resulting part's shape. This fact makes extrusion perfect for creating atypical
cross-sections and guarantees a smooth finish on the end product. Preventing waste in extrusion molding is essential, and the right mold release agent, sealer, cleaner, and lubricant for plastic molding is central to that goal. Additionally, our coating
products provide easier de-nesting of thermoformed parts which create internal cavities for extruded plastics.
Blow Molding & Packaging
Blow molding, designed for high-volume manufacturing of hollow objects, creates uniformly thin-walled products at a very low cost. It can be used to achieve shapes that injection molding can't support, but blow molding does require close tolerances where build-up on molds can interfere with, increasing waste. You owe it to your team to optimize your blow molds with Stoner mold release agents and our other related products that are designed to reduce build-up and lubricant close points.
Thermosets and Thermoplastics: The Plastic Molding Families
The plastics molding industry can largely be divided into two types of molding: Thermosets and thermoplastics. These two families of plastic molding provide unique benefits and drawbacks to the created products. When you begin your journey towards scaling production, consider what category of plastic will best fit your production needs:
Thermoset
Thermoset plastic molding typically involves injecting a mixture of materials into a high-heat mold. This heat activates a catalyst that forms a permanent chemical bond. This type of molded part typically can’t be reshaped or recycled due to the chemical process, but the result is a heat-resistant and very durable item.
Thermoset materials include:
- Epoxy
- Polyester
- Bakelite®
- Polyurethane
While these products can be very strong and durable, the byproducts of the chemical reaction are Volatile Organic Compounds or ‘VOCs.’ Dealing with these byproducts is a unique challenge for molding at scale. However, less heat and pressure is required.
Thermoplastic
Thermoplastics are, in some ways, a simpler molding material. The base materials are melted down and injected into a cold mold. This is a 100% reversible and renewable process for most thermoplastics. Thermoplastic molding produces more flexible bodies and aesthetically pleasing surfaces on molded objects.
Thermoplastics include:
- Nylon
- Polycarbonate
- Acrylic
- ABS
Thermoplastic requires high heat and high pressure, which means the machinery involved can often require a higher initial investment than other processes. Additionally, the low heat-tolerance can restrict the reasonable uses for the produced goods.
Our molding products can help you maximize your plastic molding production. Thermoplastic and Thermoset molding products can present unique challenges in demolding, cleaning, and sealing. If you are a plastic molding company looking to expand your repertoire or create at a larger scale, come to the molding products company that knows how to enhance and build upon your process.
Why Choose Mold Release Products from Stoner Molding Solutions?
You want an efficient thermoplastic molding process with less waste and downtime. To do that, you need high-quality molding products that help improve your processes. The problem is that so many inferior products that are on the market can cause you to work more and create defective parts, making you feel frustrated.
When you work with us, you receive customized service and product experience that prioritizes cost-effective products that are tailored to your manufacturing process. We understand your molding problems, which is why we have spent the last 80 years Engineering
and designing products to relieve the specific issues you face. Here’s how we do it:
Here’s how we do it:
- Talk to us about your molding frustrations—Tell us what problems you face and what specifications you have for the products you use.
- Try a free sample—We’ll send you a free sample of a recommended product so you can see if it addresses your molding challenges.
- Buy the products of your choosing—When you are convinced that our products are right for you, buy a full-size option on our website or by calling our customer service team at 1-800-227-5538.
So, get started by talking to an expert at Stoner Molding today! And in the meantime, feel free to browse our complete product listings in our plastic molding catalog.
Talk to a Plastic Molding Product Expert Today!
When you need products that can help your thermoplastic molding process run more efficiently, turn to the experts at Stoner Molding Solutions! We have various formulations that are right for your molding operations—whether you do thermoplastic injection molding, rotational molding, extrusion, or blow molding. With more than 80 years of experience, we have the products you need!
Our industry-leading experts, chemists, and engineers are here to listen and provide honest value to your business. We'll help you troubleshoot your process and recommend the right products for your needs. We can even work with you to create custom formulations tailored to meet your production requirements. All you have to do is reach out!
Some of Our Top Selling Release Agents for Plastics
Looking for more information on our top-selling mold releases? Check out these popular options! Don’t hesitate to reach out to us and explain your manufacturing process so that we can give you a product that will exactly match your needs.
Get More Information About Plastic Molding on Our Blog
The thermoplastic and thermoset molding industry is full of intricate specialties and unique molding procedures. Learn more about how to optimize your process, choose the right products, and mold more parts in less time with the experts at Stoner Molding Solutions.
Short Run Injection Molding and the Industries That Benefit from It
Many companies struggle with finding efficient ways to produce high-quality components in small quantities. Traditional injection molding processes may not be suitable due to high tooling costs, extended lead times, and the need for large production volumes.
These limitations often hinder the ability to respond quickly to market demands, leaving businesses at a disadvantage.
It’s frustrating to have a brilliant product idea or a new project that requires rapid prototyping or small-batch production, but not having the capability to produce the test product. The lengthy and costly tooling process associated with conventional injection molding can be a significant roadblock, hindering innovative product development and market entry. Production delays can result in missed opportunities and potential loss of customers and market share.
Here's where short run injection molding offers a breath of fresh air. By leveraging advanced technologies and skilled expertise, short run injection molding provides a cost-effective and efficient solution for small-scale production. With reduced tooling costs, quick turnaround times, and the ability to produce quality parts in the thousands or even just a few hundred, short run injection molding empowers companies to respond swiftly to market demands, effectively manage product development, and seize opportunities.
What Is Short Run Injection Molding?
Short run injection molding refers to a manufacturing process that specializes in producing plastic parts in small quantities, typically ranging from a few hundred to a few thousand units. It offers a cost-effective solution for companies that require rapid prototyping, low-volume production, or customized components. In this process, a mold is created, and thermoplastic materials are injected into the mold cavity under high pressure. The mold is opened once the material cools and solidifies, and the finished part is ejected.
The advantages and benefits of short-run injection molding are numerous. First, it allows for quick turnaround times, enabling companies to bring their products to market faster. This fast process is particularly advantageous for industries where time-to-market is crucial. Additionally, short run injection molding is a cost-effective solution, eliminating the need for expensive tooling and molds associated with larger production runs. Companies with limited budgets can benefit from this approach without compromising on quality. Furthermore, this process allows flexibility and agility in design iterations and product improvements, making it ideal for companies that value innovation and adaptability.
Which Industries Benefit the Most from Short Run Injection Molding?
Short run injection molding finds application in various industries. Still, four key sectors stand out for reaping significant benefits from this manufacturing process: the automotive industry, the electronics industry, the medical device industry, and the packaging industry.
THE AUTOMOTIVE INDUSTRY
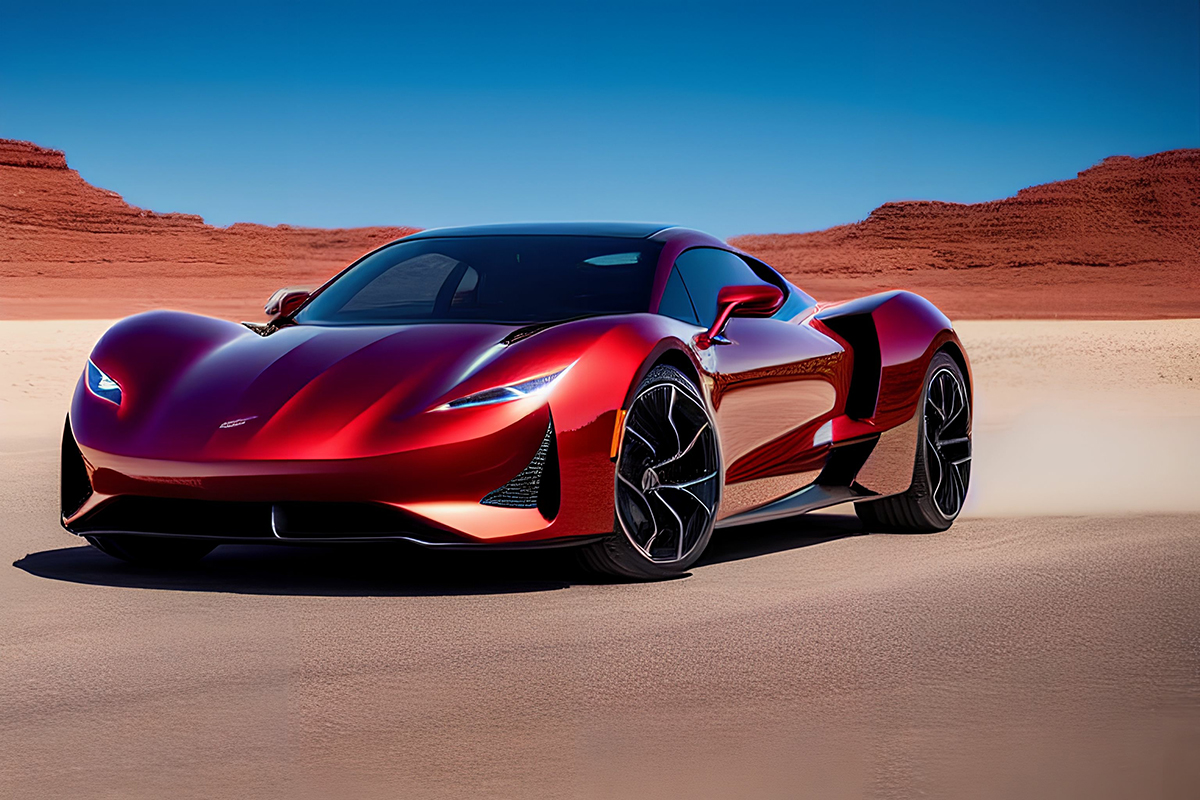
In the automotive industry, short run injection molding plays a vital role in customizing parts for specific models. It enables manufacturers to produce limited quantities of high-quality components with precision, ensuring a perfect fit and finish. This top-tier quality is particularly valuable for luxury and exotic car manufacturers who offer high-end vehicles in limited numbers. By leveraging short run molding, they can maintain exceptional quality standards while meeting the demand for exclusivity.
THE ELECTRONICS INDUSTRY
The electronics industry benefits from short run injection molding through rapid prototyping and quick production of consumer electronics. This fast-paced process allows companies to test and validate product designs before committing to large-scale manufacturing. Unlike 3D prototyping, which often limit sample quantities, short run molding offers the ability to produce more samples in less time, providing greater flexibility for design iterations and improvements.
THE MEDICAL DEVICE INDUSTRY
In the medical device industry, where stringent regulations and precision are paramount, short run injection molding accelerates the development process for medical devices. It enables cost-effective production of small-batch components, making it suitable for niche applications or specialized medical devices that require limited quantities. Short run molding ensures high quality and reliability while meeting tight timelines and maintaining compliance with regulatory standards.
THE PACKAGING INDUSTRY
The packaging industry benefits from short run injection molding by enabling the creation of unique packaging designs for limited-edition products. It allows companies to meet specific packaging requirements for new product launches, ensuring eye-catching and functional packaging solutions. Short run molding provides the flexibility to produce a limited number of parts while keeping options open for future design changes or additions.
Factors for Using Short Run Injection Molding Solutions
When considering short run injection molding solutions, several factors come into play. These include cost factors and budget considerations, design limitations, material selection, and the use of the right molding products.
COST FACTORS & BUDGET CONSIDERATIONS
Short run injection molding offers cost advantages compared to larger production runs. Since fewer parts are required, less expensive mold materials such as aluminum or lower steel grades can be used, reducing tooling costs. With lower upfront costs, short run injection molding becomes accessible to a broader range of customers with smaller budgets. Additionally, adjustments and modifications can be made without significant financial commitments, and prototypes may require less finishing than in 3D printing, saving both time and cost.
DESIGN LIMITATIONS & MATERIAL SELECTION
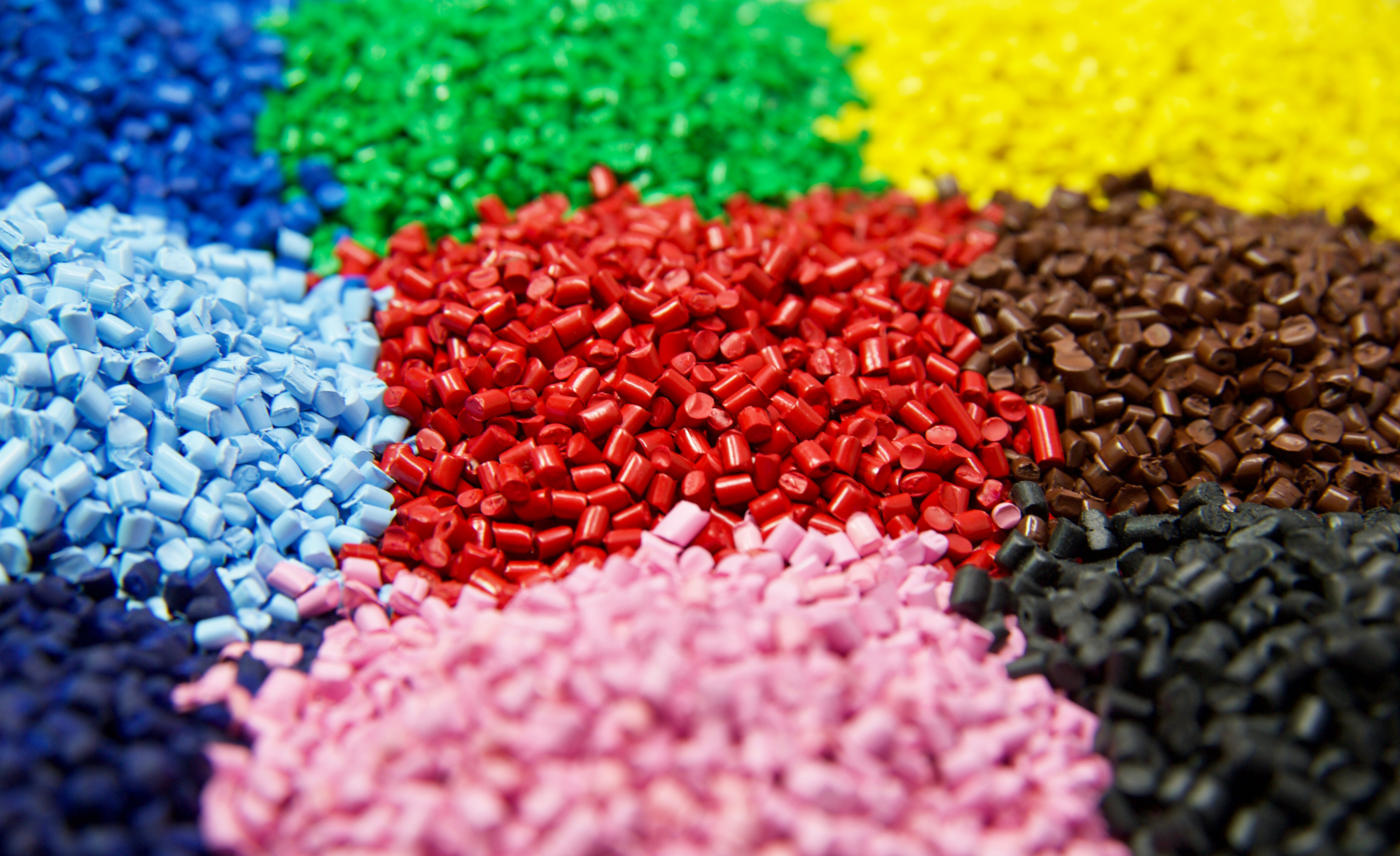
Short run injection molding does not significantly restrict resin requirements due to the mold material. It allows for utilizing a wide range of resins available in higher volume molding processes. Material selection plays a critical role in determining the final product's quality, durability, and performance. Factors such as environmental conditions and specific requirements need to be considered when choosing the appropriate material. By carefully selecting the right material and considering design limitations, companies can ensure that the chosen material meets all necessary requirements while remaining cost-effective.
USING THE RIGHT MOLDING PRODUCTS
Utilizing the right molding products is crucial to enhance the short run injection molding process. Mold sealers are commonly used to fill in the microporosity of molds, resulting in an even finish on the molded parts. Mold release agents aid in easily releasing items from the mold after the molding process is complete. Mold cleaners help maintain the cleanliness and longevity of molds, ensuring optimal performance over multiple production cycles.
By considering these factors and leveraging the benefits of short run injection molding, companies can achieve efficient and cost-effective production for their customized components prototypes.
Need Help with Your Molding Operations?
Short run injection molding provides a game-changing solution for companies seeking efficient and cost-effective manufacturing processes for small-scale production. We have explored the numerous benefits of this innovative technique, from its ability to meet the demands of various industries to its flexibility in customization and rapid prototyping.
By leveraging our advanced products experienced team, and commitment to excellence, we aim to make your production processes more efficient, cost-effective, and responsive to market demands. Contact us today to explore how our short run injection molding products can empower your business to create precise, high-quality parts quickly and easily.
Resources:
· https://www.bennettplastics.com/the-benefits-of-short-production-run-injection-molds